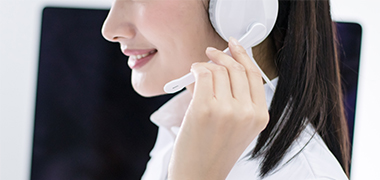
- Contact:Minister Xu
- Mobile:13841408476
- Tel:024-44837288
- Fax:024-44837004
- E-mail:xuming58@126.com
- Web:natashaterry.com
- Address:No.110 XiangHuai Road
Benxi Economic Development Zone
Liaoning Province
The Customer-First Mindset Behind Timken’s Award-Winning ES302 Coating
16 Oct,2019
Back in the late 2000s, wind energy farms in the United States found they had a problem. The wind turbines they had installed in the late 1990s or early 2000s—designed to produce electricity for 20 years—were in desperate need of major mechanical overhaul.
The roller bearings in turbine main shafts and gearboxes were experiencing premature damage relative to their design intent. Fixing these problems required a major rebuild, at a cost of up to $300,000 every time they failed, or an estimated $1.2 million over the lifespan of a turbine.
About this same time, a research and development (R&D) team at Timken had reached production stage on a plasma coating process for roller bearings that had been in the works since the late 90s. “When we first started researching how coatings could impact tribological performance in rolling element bearings, we were trailblazers,” says Ryan Evans, who came on as an undergraduate in chemical engineering to work on the project and currently serves as director of R&D for bearings.
“You never want the steel surfaces to touch in a bearing,” he says. That seems like a tough demand because when you look at a roller bearing, you see rollers moving around in a tight space. But that’s the reason for lubrication—so there’s always a film between the roller and the inner raceway ring.
Unfortunately, lubricant films are difficult to maintain consistently. Early wind turbine designs, for example, often included two-row main shaft spherical roller bearings (SRB) which had to support a radial reaction and wind thrust loading on only the downwind row of rollers. As the bearing wore because of that uneven pressure, it transferred increasing axial deflection loads to the gearbox bearings. Wind energy companies found it challenging to keep the bearings lubricated well enough under these complex loading conditions to avoid damage.
Solving for steel-on-steel
Many heavy industries face that steel-on-steel contact problem within bearings. To solve it, the Timken team adopted a novel approach: making bearing rollers less “steel-like” than the rings. “We put a super-thin—fractions of a human hair thick—layer of a composite material on them,” says Evans. “It’s an engineered combination of ceramic and a polymer, or in other words, a plastic-like thin layer of material full of tiny ceramic particles.”
Essentially, the coating that Timken developed—dubbed ES302—was both hard and wear-resistant like a drill bit and yet slippery and nonstick like your favorite fry pan. The company found a healthy aftermarket strategy in replacing wind turbine bearings with wear-resistant SRBs featuring the ES302 coating on rollers.
Agriculture was another early market for wear-resistant bearings in large farming implements, such as tractors and combines. Aerospace customers also found applications, along with paper mills, oil and gas companies, mining companies, and others.
Today, Timken coatings are a premium product option. “You can add them to any of your favorite Timken bearings, generally speaking,” says Evans. “If you’ve been buying one bearing and you like it, but you’d like it to last longer when lubrication conditions are poor for whatever reason, we can add the coating without having to redesign the whole thing entirely.”
An entrepreneurial R&D mindset
Evans looks back fondly on those ES302 development years. The core team was a tight-knit group that also included Gary Doll, now Timken professor of surface engineering and director of the Timken Engineered Surfaces Laboratory at the University of Akron; Jim Gnagy, product development specialist; and Tim Springer, program manager. In the years leading up to the ES302 project, other Timken R&D engineers and analysts made valuable contributions in developing Timken wear-resistant technologies as well.
“We traveled the world talking about advanced coatings technology and wear-resistant bearings with customers,” Evans says. Direct customer contact was key. He attributes much of the product’s success to the opportunities the team had to uncover real-world challenges, building relationships with customers and testing and getting feedback on solutions out in the field.
“For that original startup period, it was very much R&D right in front of customers and developing it quickly,” he says. “We would send them prototype parts and then wait to hear back.” It was always satisfying to receive an email message from the field along the lines of, “It just crossed the 2,000-hour threshold!” for a part that had never lasted longer than 200 hours previously.
International recognition
Bearings may not be the first thing most of us think about when we consider the technology that enables modern civilization, and yet every machine with rotating parts requires them. Ultimately, Timken coatings have succeeded simply because they help bearings do their hidden job dependably, without anyone being the wiser.
“We put a wear-resistant bearing with coatings on it out in the field and rarely hear from the customer again,” says Evans, “except to get orders for more the next year, and the next.”
“ES302 has opened doors and helped us grow in industrial bearings for challenging applications,” he says.
In 2017, ASM International, the preeminent materials information society, recognized Timken with its prestigious Engineering Materials Achievement Award for ES302’s “significant contributions to the field of materials science and evidence of industrial impact.” Previous winners of the annual award, established in 1969, include GE, Northrup Grumman, IBM, Boeing, and GM, to name a few.
For the development team, it was a proud moment. “We get commercial validation every time we sell Timken Wear-Resistant products,” says Evans. Accepting the award brought home a broader sense of how much their customers and technical peers appreciated the work that went into developing ES302.
Customers at the core
Today, Timken researchers are looking for ways to reduce coating costs and make engineered coatings more accessible to a wider variety of customer applications. “Coatings today can be expensive relative to the bearing cost for general high-volume industrial or automotive bearings. What if we are able to achieve the same wear-resistant performance out of a coating that costs less?” says Evans.
“Timken is partnering with centers of excellence worldwide to help solve these challenges,” he says. That includes local institutions, such as the University of Akron, where Doll is working on the next generation of coating technologies.
Materials and processes may shift over time, but in the years since developing ES302, Evans has come to understand how important that customer collaboration mindset is for Timken, across the product line.
“We have thousands of unique parts you can buy from us,” he says. “That’s evidence that Timken engineers have gone out and worked with customers on the problems they care about.”
“We invest in R&D to identify fundamental problems in our customer’s applications, to work on the cutting edge of engineering and scientific knowledge to solve them, and then to apply the solutions across multiple industries,” he says. “Wear-resistant coatings are a great example of how we worked together to create value over time, from the lab all the way to our customer’s equipment.”