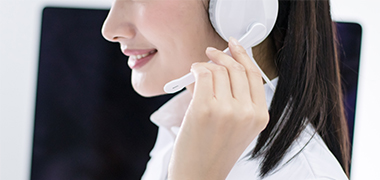
- Contact:Minister Xu
- Mobile:13841408476
- Tel:024-44837288
- Fax:024-44837004
- E-mail:xuming58@126.com
- Web:natashaterry.com
- Address:No.110 XiangHuai Road
Benxi Economic Development Zone
Liaoning Province
How to give end users remote connectivity
14 Oct,2019
In this sponsored content, we talk with Ben Fogg of Fogg Filler owner alongside Ola Wesstrom, senior industry manager—food and beverage at Endress+Hauser
Fogg Filler designs and manufactures rotary filling, rinsing, capping and enclosure systems. Fogg serves a growing number of dairy, water, food and beverage, pharmaceutical and consumer product goods companies around the world.
Fogg was founded in 1956 by Clyde Fogg, who had been assembling, selling and servicing Cherry Burrell equipment for 22 years prior to starting Fogg. As new containers were developed, Clyde rebuilt machines, while adding his own ideas and improvements. When plastic was introduced, Fogg was among the first to modify machines to handle plastic jugs—new valves, cappers and bottle-handling equipment also had to be developed and incorporated into existing dairy fillers.
In 2000 Fogg’s son, Mike Fogg, became the sole owner, and in 2003 his son, Ben, came onboard, bringing a strong background in chemical and mechanical engineering and opening new doors to new cutting-edge ESL technology. In 2008, Ben Fogg became the sole owner, continuing the family business for the third generation.
In serving the global marketplace, Fogg designs and manufactures filling systems, as well as related equipment for specific applications, combining skilled craftsmanship with innovative management to offer customers a quality team.
Fogg Filler supplies products and services designed to bring customers improved profit margin, which will in turn allow shareholders and employees to prosper. Ben Fogg, owner, and Ola Wesstrom, senior industry manager—food and beverage at Endress+Hauser, shared their thoughts on remote connectivity.
Q: There are ways to provide remote access into plants’ processes. If a customer was interested in allowing remote access, how would OEMs like Fogg Filler be able to support?
A (Fogg): Fogg Filler offers several ways to remote into customers’ processes, including virtual private network (VPN), EWON and SECOMEA. The VPN enables us to go directly into our customers’ network. EWON provides a window between us and our customers through the cloud. SECOMEA provides a window between us and the customer through the cloud, as well, but it has similar security to a banking system. This seems to be the preferred method for most customers, if they allow us access.
Q: What are the customers’ benefits, if they allow OEMs to remotely connect to their process?
A (Fogg): If remote access is enabled, we can create a private Web page for our R&D team to access the customer’s data. This allows our team to test and monitor new technology to better serve customers.
If a customer is experiencing a challenge and needs assistance troubleshooting, the customer typically requests one of our technicians to come visit the site. This approach can cost thousands of dollars, as travel expenses add up. With remote access, we can troubleshoot the machine, change programming and add new recipes right from our office. It is an efficient way to help our customers with their challenges and reduce expenses.
We can collect data for our customers and provide reporting details back to them. For example, we can collect data on maintenance items such as runtime of UV bulbs. There are warning screens on the filler, but, if an operator bypasses them to keep running, you wouldn’t know. We collect the data and send the information via text or email to the proper people for re-order. We can set monitors on all motors that detect vibrations to indicate when bearings need to be replaced—a preventive approach, so customers can re-order before a failure occurs. The options in this area are endless.
If our customers have Endress+Hauser meters installed in the process, we can monitor them remotely, as well. Most often, a customer will call us if the equipment isn’t running properly, even if the issue is with the meter.
Endress+Hauser has the capabilities to monitor this, but, if they call us, we would have the information and would be able to assist. This allows us to remotely troubleshoot issues efficiently and proactively.
When a customer requests an on-site visit, our technicians can download the current program they use prior to the visit.
Q: Remote connectivity seems like a benefit, but some customers tend to hesitate to allow remote access into their process for security reasons. What are companies doing to ensure trust, security and safeguard customers’ information?
A (Wesstrom): Operational security is of course of primary importance. By connecting instruments to an edge device, actionable health and diagnostics information can be sent to the cloud in a one-way communication, thus preventing anyone getting access to change any parameters. The Endress+Hauser Netilion platform enables this in an easy and cost-efficient way.
Q: You mentioned Endress+Hauser’s Netilion platform. Would you describe what it is and the benefits customers would receive from it?
A (Wesstrom): Netilion is Endress+Hauser’s customer IIoT solution. It is an ecosystem that comprises a multitude of elements, such as digital services and products as well as cloud-to-cloud connectivity for users and partners. The coexistence of all these elements creates added value for the users. Netilion digital services are Scanner, Analytics, Health, Library, Value and Predict.
Q: What advanced technologies do Endress+Hauser and other manufacturers offer that OEMs can take advantage of?
A (Wesstrom): To identify the root cause behind performance issues or downtime, it is important to be able to access instrument-specific diagnostics and second or third variables that can help to identify or eliminate issues during troubleshooting. This is made possible by accessing the diagnostics and verification functions remotely. This information can be accessed via the control system or via gateways.
Q: What are some of Endress+Hauser’s latest innovations that the food and beverage industry should consider?
A (Wesstrom): One of the most revolutionary advancements in temperature measurement is the TrustSens technology that enables automatic calibration of temperature sensors each time a predetermined temperature, say, 245 oF, is traversed. This ensures that the measurement is always within defined tolerance. Value to the user is reduced risk and associated costs if the measurement sensor drifts one day after manual calibration. What is the process or cost impact by waiting to find out until next manual calibration cycle?
Q: What’s the latest cost-efficient offering from Endress+Hauser that the food and beverage industry should consider?
A (Wesstrom): Process diagnostics and OEE monitoring rely on existing instruments but often also need additional points. To reduce the cost impact of adding these points, Endress+Hauser has added several entry-level-style instruments, such as the Nivector FTI26, to the product basket. These $150-$500 instruments make it possible to collect information via traditional means or digital networks such as IO-link and are IoT-ready.