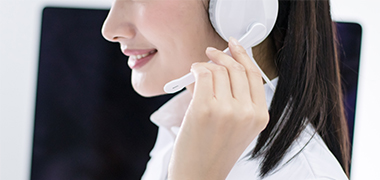
- Contact:Minister Xu
- Mobile:13841408476
- Tel:024-44837288
- Fax:024-44837004
- E-mail:xuming58@126.com
- Web:natashaterry.com
- Address:No.110 XiangHuai Road
Benxi Economic Development Zone
Liaoning Province
What is the best maintenance strategy for bearings?
28 Aug,2019
Over time, even the best bearings will begin to wear down and fail without proper attention. A set bearing maintenance strategy can help you identify issues and avoid unnecessary downtime. Of course, the strategy that’s best for you can vary depending on your applications and upkeep needs. When it comes to bearings, there are three general maintenance strategies that apply: periodic, predictive, and run-to-fail.
Periodic preventative maintenance relies on, unsurprisingly, a periodic maintenance schedule. This practice is based on setting regular intervals for you or someone on your team to clean, inspect, and fix up the bearings found in your applications. The schedule can vary from appliance to appliance depending on need and ease of accessibility of your equipment. This maintenance strategy is great for businesses where wear and tear are normal and can’t afford to risk any chance of downtime.
While periodic maintenance is set on a hard schedule, predictive maintenance creates a schedule to try and identify signs that your equipment requires maintenance. For example, you may have a schedule to check your equipment every other month, either by manual inspection or monitoring technology. If you or a member of your team notices excessive vibration, overheating, leaks, misalignment, or any other warning signs, it’s time to shut down that application to repair or replace your bearings or any other problem parts. If there are no signs of issues, you can hold off on repairs or replacements until the next inspection. This style is good for businesses that don’t want to risk downtime, but may not need to fix or replace bearings too frequently.
A run-to-fail strategy isn’t so much a maintenance plan as much as a decision to not perform any repairs or replace any parts until something is wrong. This approach isn’t the best strategy for bearings that can be re-lubricated or repaired before failure, but it may be a more realistic options for businesses that can either accommodate unplanned downtime or have out-of-reach equipment where regular maintenance is impossible or too costly. For example, if equipment failure won’t affect production and downtime can be kept at a minimum, a run-to-fail approach may be more cost-effective in the long term.
Ritbearing
www.ritbearing.com