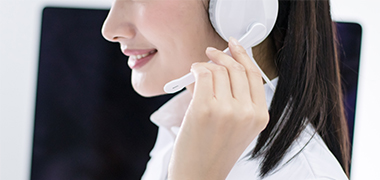
- Contact:Minister Xu
- Mobile:13841408476
- Tel:024-44837288
- Fax:024-44837004
- E-mail:xuming58@126.com
- Web:natashaterry.com
- Address:No.110 XiangHuai Road
Benxi Economic Development Zone
Liaoning Province
How to select bearings for submarine applications
05 Aug,2019
Submarine life is not easy. Historically, these vessels would stay underwater for just a few days, before resurfacing to exchange stale air for fresh oxygen. Today’s submarines however, use oxygen systems to enable travel for up to 90 days at a time. Here Chris Johnson, managing director of SMB Bearings, explains how to extend the lifespan of components in these vital air purification systems.
Air purification systems are vital to maintaining human life in a submarine. The systems release oxygen based on the percentage in the air, or in traditional systems, the oxygen is released periodically. Bearings are used to enable the flow and distribution of oxygen from fans in these systems, after releasing the gas from pressured tanks, generators or canisters.
What could cause these bearings to fail?
Bearings in these environments are often exposed to harsh chemicals and solvents. If the incorrect bearing material and grease are selected, these environments can severely damage the bearing. SMB Bearings recently completed a project to replace the bearings in a submarine’s air purification system. The previous bearings were incorrectly lubricated with non-chemically resistant grease. Because of this, the solvent in the system was stripping grease out of the bearing while in operation.
Incorrect lubrication may not always cause a catastrophic or sudden failure in a bearing. However, it could cause the bearing to last a fraction of the time required, due to damage from chemical exposure. This was the case here — a dangerous risk when 800 feet under the sea.
Before changing the grease in a bearing, selecting the correct bearing material should be considered a priority. In environments like these, standard steel ball bearings will often suffice as the solvent is not corrosive. As an alternative, some choose 440 stainless steel bearings. The material is often selected for use in mild chemical environments, whereas 316 stainless steel bearings or ceramic bearings are usually the best option for aggressive environments. For low precision applications, plastic bearings are also an option.
Acetal resin bearings are a type of plastic bearing which use acetal resin rings and nylon cages. These are often supplied with 316 stainless steel balls or glass balls. These bearings cope well against exposure to alcohol and chlorides, as well as good resistance to acids and alkalis. Full ceramic bearings have excellent corrosion resistant properties and, with their ability to operate without lubrication, are widely used in marine environments.
For the submarine air purification system, the solution was to re-lubricate its existing bearings with a non-toxic, chemical resistant grease. While it is not highly publicised, many standard bearing greases are incompatible with certain chemicals. Not only is this important for bearings in air purification systems, but also for any equipment in which harsh chemicals are present. This includes cleaning equipment, chemical processing equipment and chlorine systems.
For a submarine’s air purification system, failure to distribute oxygen — even by a small percentage decrease — could disrupt the balance of gases to a life-threatening level. Similarly, the air purification system should also ensure the removal of the moisture cause by human breath, and the concentration of carbon dioxide in the air. If carbon dioxide is not removed, it can become a life-threatening toxin once it reaches high levels.
Most submarines have advanced technology to identify even the smallest discrepancy in oxygen supply. This enables engineers to recognise any problems quickly. However, rather than following a repair-and-replace model, establishing a system that can withstand solvents and chemicals will lower maintenance costs.
This is not only pertinent for air purification systems, but for any equipment used in chemical environments. This is particularly applicable for machinery in pharmaceutical and chemical industry bearings. By selecting bearings and grease that withstand harsh chemicals, engineers are assured that the bearings will function effectively, without experiencing ongoing damage from their operating environment
Air purification for submarines ensure that the vessels can withstand underwater operation for up to 90 days at a time. While a bearing may seem like a tiny component in these large, complex systems, their functioning is vital to the equipment’s operation, and the lives of those on board.