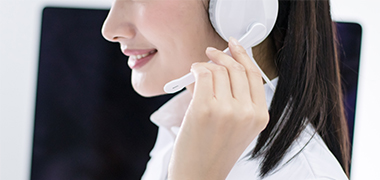
- Contact:Minister Xu
- Mobile:13841408476
- Tel:024-44837288
- Fax:024-44837004
- E-mail:xuming58@126.com
- Web:www.natashaterry.com
- Address:No.110 XiangHuai Road
Benxi Economic Development Zone
Liaoning Province
Roller bearings for longer turbine lifespans
05 Aug,2019
Thyssenkrupp Rothe Erde's single momentum rotor bearings are incorporated in large-scale direct-drive and geared turbines, and they will soon enter the 10MW offshore range. Eize de Vries talks exclusively with senior engineers about the company's latest product and R&D advances, and visits its massive new outdoor rotor and pitch bearing test rig.
Over the past decade, Thyssenkrupp Rothe Erde has developed between 40 and 60 taper-roller rotor- or momentum-bearing prototype designs, says Jan-Peter Bochert.
He is part of the product engineering bearings group, which is responsible for advanced simulations and calculations on the latest large-scale designs.
All Rothe Erde bearings are tailor-made solutions, although they mostly feature a symmetric layout with a 45-degree roller-contact angle.
The largest units currently deployed — exceeding 3.5 metres in outer diameter — are incorporated in a 6-8MW direct-drive offshore turbine series.
"In late 2016, the company re-equipped the Lippstadt plant [in the north-west German state of North Rhine-Westphalia,] with new production machinery aimed at the next-generation of 10MW-plus offshore turbines that require matching single rotor bearings in the 6.5-metre range," says Bochert.
"However, we refocused our scaling strategy last year, and our aim is now to increase load capacity and lifetime while keeping down bearing dimensions at the same time."
Asymmetric move
This new approach was enabled by switching from a symmetric baseline design to an asymmetric layout with a reduced upwind (rotor-facing) roller-contact angle in parallel with increasing roller length.
Bochert says this scaling and optimising process was carried out in two main steps, concluding with reducing the upwind roller angle from a 45-degree baseline value to 35 degrees, while increasing the length of the roller by 20%. The downwind raceway remained unchanged.
"The most remarkable outcome was a combined 50% increase in upwind and downwind roller raceways lifetime performance, with only a 15% increment in bearing mass," says Bochert.
"We have also been able to retain the bolt-circle diameter of the original bearing, while only slightly increasing the height. It means this asymmetric layout with almost unchanged dimensions from the bearings fitted in 8MW direct-drive turbines can now accommodate the latest 10MW designs."
A key contributing factor for the enhanced bearing lifetime was a big reduction in maximum roller-raceway contact pressure in both raceways.
And because bearing calculations inherently always consider deformation, deep insight regarding loads and load-distribution patterns is crucial.
"This necessitates the optimal matching of all interfaces between the bearing and rotor support structure, gearbox and/or generator, and all combined interface linkages between hub and blade bearings and blades," says Bochert.
"All these interaction aspects regarding stiffness and deformation behaviour must be addressed and, if necessary, adapted during the various turbine design stages."
Bochert cites another example. The company supplied the rotor bearing for a 3MW medium-speed geared turbine with a 100-metre rotor.
Further development of this turbine concept resulted in a 145-metre rotor, more than doubling the swept area, and a slightly enhanced rating of 3.2MW.
The original bearing (bolt circle) of about 2.5 metres could be retained by adapting the design for optimised load distribution and enhanced load capacity.
"An integral approach and optimal systems integration is key to achieving robust and long-lasting bearing solutions," says Bochert.
"This requires close cooperation and full transparency between us as the bearing supplier and the OEMs to go through all necessary iterative design steps together during turbine and bearing joint development."
Complex conditions
An in-depth understanding of bearing-roller behaviour under complex dynamic operating conditions is a key enabler for the development of increasingly larger bearing, points out Bernd Lüneburg, the company’s head of research and development.
To address these challenges, the firm developed its ingenious in-house diagnostic roller-measurement technology.
This is based on an "intelligent" single measuring roller per bearing, a principle fit for any new future bearing under development.
"A double-row taper-roller bearing for a large-scale turbine contains rollers that each have a 60-100mm diameter," says Lüneburg.
"One integral aspect of the measuring roller technology concept is that it always uses in-house produced rollers from the same batch."
Each individual measuring roller incorporates a sensor for real-time measuring of deformation at two axial positions, plus slippage, tilting, temperature, velocity and relative circumferential position.
Each roller further contains a tiny permanent-magnet generator with internal power and data storage capacity, supplemented by wireless signal transmission, adds Lüneburg.
The system is designed for long-term operation and measures all the characteristics mentioned above per roller row without losing any bearing-loading capacity.
The technology combines Rothe Erde’s bearing and measuring expertise, and is validated at an in-house test rig.
These tests include the evaluation of roller tilting and non-symmetric roller pressure distributions, and the measuring of roller forces compared to calculated values all around the raceway circumference.
Hydrostatic support
"This is an exciting project, and very important in allowing accurate measurements at a fundamental level inside bearings.
"The technology is still being optimised, but it is already integrated in our bearing-development processes and prototyping," says Lüneburg.
"It will enable better system understanding, including on critical interfaces and bearing loads distribution, speed up working towards validation, make more accurate lifetime prediction and, ultimately, develop more compact and less expensive bearings."
Rothe Erde’s latest semi-integrated hybrid bearing technology has reached an advanced conceptual study phase.
The principle combines a "conventional" oil-lubricated momentum bearing bolted to a hydrostatic support bearing in front, facing the rotor.
The modular-design hydrostatic part’s inner ring contains multiple highly flexible and easy-to-exchange hydrostatic elements (stamps) incorporated all along the circumference at, for example, a 45-degree inclination.
Together, these apply constant oil-driven pressure against the outer rings. The oil film between the stamps and outer ring is retained through hydrostatic pressure.
"The main motivation behind this innovation is that future large-scale drivetrain designs beyond 10-12MW require more flexible design approaches to avoid steep head-mass increment," Lüneburg explains.
"The combination of higher rating and larger rotors also inevitably leads to increased loads and deformations. This, in turn, could result in main component sizes becoming critical for production, transportation, site-assembly and operating reliability."
Tilting moments
A reduction of component sizes, together with stiffness optimisation, have therefore become key wind industry targets, he adds.
The company has already completed a "proof of concept" test rig comparison between a scaled hybrid prototype and a conventional moment bearing, with promising results.
These included a doubling of conventional bearing lifetime while, in parallel, allowing a 20% reduction in bearing diameter with unchanged bearing loads.
These favourable outcomes are achieved through much-reduced rotor-induced tilting moments in the roller-raceway interfaces, which allows lower roller pressure, roller forces and internal bearing deflections.
"Integrating the Rothe Erde hybrid main bearing in existing or new turbine designs offers enhanced total drivetrain stiffness with only minor conceptual changes to the turbine, and it offers a fail-safe solution," says Lüneburg.
"In the event of oil pressure loss, the turbine can continue operating at full power — only temporarily consuming more bearing lifetime — until the problem has been fixed.
And, because the hydrostatic-bearing oil pressure can be regulated, the solution offers a unique extra control option — adapting stiffness or damping behaviour at turbine systems level."
The next steps envisaged are a full-scale prototype of a hybrid main bearing, with test-rig verification starting before the end of the year.
This will be followed by a field test with a client prototype, for which no starting date has yet been set.
Out in the open — Outdoor test rig for large bearings ready for 12MW-plus turbines
Thyssenkrupp Rothe Erde has commissioned its open-air modular-constructed test rig for pitch and rotor bearings up to six metres in diameter, fit for 12MW-plus turbines.
It was built at an industrial site around 10km from Lippstadt and comprises a huge, flat "three-legged" concrete structure with an elevated central hub mounting area.
The key principle is to mount original turbine hubs with matching original momentum bearing, pitch bearing and one original blade on it. The current test arrangement is a shortened 75-metre offshore blade extending over the long leg, but with ample space remaining to mount much longer blades in future.
Steel pipes with comparable key characteristics are fitted to the other blade-bearing positions.
The test bench is equipped with three large-scale hydraulic cylinders, each capable of pivoting and applying pre-programmed tensile forces to the blade and steel pipes to perform real-life testing.