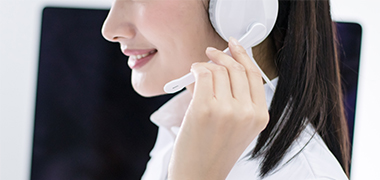
- Contact:Minister Xu
- Mobile:13841408476
- Tel:024-44837288
- Fax:024-44837004
- E-mail:xuming58@126.com
- Web:natashaterry.com
- Address:No.110 XiangHuai Road
Benxi Economic Development Zone
Liaoning Province
Bearings Help in Optical Inspection Equipment Application
31 Jul,2019
Nearly a decade ago, a manufacturer of optical inspection equipment came to us with a dilemma: Its equipment was having problems, well, focusing.
Despite incorporating state-of-the-art technology into the product’s overall design, the focusing mechanism was underperforming. It wasn’t a reflection of the lens itself, whose materials and workmanship were industry bests. Rather, as the overall mechanism required smooth, incremental movements powered by a minuscule motor, it was highly susceptible to the slightest variations in starting torque. This made it a bearings issue.
AST initially introduced higher precision catalog bearings, but the motor couldn’t generate sufficient power to drive the mechanism consistently. Additionally, despite a reduction in fill amount down to 10%, adding the requisite grease lubricant created drag that compromised functionality.
That’s when AST engineers came up with a solution — use ceramic balls inside of the stainless steel rings to run the bearings without any lubrication. Typically, a bearing should run with lubrication, but in this case, the ceramic balls’ lightweight quality and high polish helped to reduce torque without the need of lubrication (which had been causing drag). Additionally, engineers trimmed the bearing’s ball complement from 13 to only five, while achieving precision and consistent movements with the focusing mechanism. The entire design took roughly nine months to complete, a process that included multiple levels of samples. After significant trial and error, AST arrived at a version that, nine years later, continues to perform.
AST’s in-house capabilities, including a clean room, proved critical to the project’s success. The ability to disassemble the bearings, replace the steel balls with ceramic balls, re-install the retainer, and perform the final inspection in a cleanroom environment made the entire process turn-key for the manufacturer, a rarity in the bearings industry.
This custom bearing assembly is still manufactured today, completely in-house (assembly, processing, cleaning). It has proved exceptionally durable while delivering uniformly consistent results.
When trying to find a bearings solution that minimized torque, engineers reduced the ball count and turned to ceramic balls, a lightweight material with a very high polish, which collectively reduced torque. Additionally, the dissimilar ring materials allowed the bearings to run without lubrication.
AST
www.astbearings.com