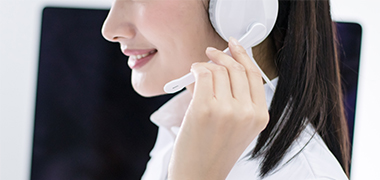
- Contact:Minister Xu
- Mobile:13841408476
- Tel:024-44837288
- Fax:024-44837004
- E-mail:xuming58@126.com
- Web:natashaterry.com
- Address:No.110 XiangHuai Road
Benxi Economic Development Zone
Liaoning Province
AST Lubrication and Bearings Help in Extreme Weather Application
19 Jul,2019
A middle market OEM that produces outdoor electrical cabinets had a problem: With many of their cabinets located near coastal areas, weather exposure, including salt from ocean spray, was compromising the integrity of its products, which incorporated bearings on the cabinet hinges. Specifically, condensation had rusted the cabinet’s ball bearings and steel cage.
Historically, they had used a conventional catalog chrome steel bearing for its cabinets, which was incapable of withstanding the coast’s extreme weather variations — which often occurred on the same day. Servicing the corroded bearings was difficult, as the cabinet hinges had frozen, making it difficult to even open the cabinet.
The manufacturer approached AST to find a cost effective and efficient solution, and the AST team responded by first addressing the basics: grease. While a new lubricant provided short-term relief, it quickly became evident that this was not a long-term solution. The internal metal components still became corroded and non-functional.
Next, AST engineers transitioned production to full stainless steel bearings, which provided the cabinets with the desired functionality and durability — but at a cost that was prohibitive. In total, the new bearings cost at least four times more than the original bearing, which made repair and new production costs too high.
AST engineers went back to work, tinkering with various material options while understanding that many of the cabinets were still active (in operation near the sea), which rendered prospective design changes impractical.
After a review of their faulty bearings, the team honed in on the common damage: While grease protected the raceway surfaces of the rings, weather had rusted the soft metal cage and the balls. The engineers considered this narrower damage and concluded that a revised stainless steel ball complement and assembly inside a standard chrome steel ring set would provide the necessary product improvements.
After three months of design and testing, including comprehensive failure analyses, AST arrived at a fully functional solution: a customized 6209-2RK ball bearing with chrome steel rings, stainless balls and cage, double lip labyrinth seals and aluminum complex grease.
The components deployed easily into existing cabinets that were already in the field, replacing their existing hardware. The setup was cost effective, too, adding just 15% to the cost of the original. Moving forward, it became the standard setup for the company on all new cabinets that it produced, integrating seamlessly into the existing manufacturing process.
AST-DW-Image2Combining stainless steel balls with a chrome steel ring (rather than chrome with chrome) is unusual and certainly not obvious, which made the AST design process a case study in thinking outside the box. And it’s this ability and willingness to assess a problem and consider customer limitations before developing a solution that distinguishes AST as an industry leader in ball bearing technology.
Additionally, AST has developed a global network of partner manufacturers who will produce customized designs — again, unusual in the industry — ensuring the optimal performance of its customers’ products.
Several years after the production modification, the manufacturer continues to integrate AST’s customized 6209-2RK setup into its cabinets, to great success: Its products last longer, they cost less to maintain and repair and as a result, they have realized a healthier bottom line.