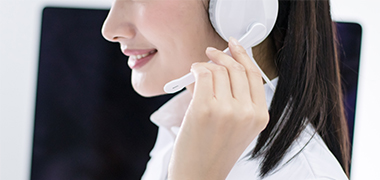
- Contact:Minister Xu
- Mobile:13841408476
- Tel:024-44837288
- Fax:024-44837004
- E-mail:xuming58@126.com
- Web:natashaterry.com
- Address:No.110 XiangHuai Road
Benxi Economic Development Zone
Liaoning Province
Customised and hybrid bearings solve fundamental issues in electric vehicles
08 Jul,2019
The high speed of the electric motors used in EV&HEV powertrains requires the use of customised bearings. Ceramic ball bearings are most capable of dealing with all the specific conditions, says Anthony Simonin, EV and HEV Competence Centre Manager at SKF.
Gothenburg, Sweden, 17 May 2019: On the surface, there appears little difference between an electric and hybrid vehicle (EV&HEV) and the conventional car, powered by an internal combustion engine, that it will increasingly replace.
However, beneath the chassis, the gulf is huge, with the most fundamental shift being in the drivetrain. Here, powerful electric motors provide the power, and the way in which they work, and how they connect to the rest of the car, requires critical components such as bearings to be redesigned or adapted to work in this new environment.
For instance, the motor itself must run at very high speed, far faster than it would in a conventional industrial application, meaning that bearings within it must be able to cope without failing. In general, this has been solved by adapting conventional steel ball bearings, such as by redesigning the cage and using special lubricating grease.
A typical EV uses up to four motors, if each is connected to a separate wheel. These run at up to 30,000rpm, which is around three times the speed of a typical industrial motor. This puts an enormous strain on the internal bearings, so these will need to be replaced or adapted.
One way is to redesign the bearing and the polymer cage, adapting the fundamental design. This ensures that the overall bearing configuration can withstand the higher speed, acceleration and temperature that we can see in these applications.
In addition, the higher speeds require more efficient lubrication. Here, special greases are required that can keep their viscosity and so continue to be effective lubricants at these higher speeds and temperatures.
While the electric motor, in combination with an inverter, ensures high efficiency, there is one feature that can affect conventional steel bearings. The high-frequency voltage switching of the inverter, which in turn causes current leakage. The current can end up being conducted through the bearings. This can cause problems such as surface pitting, and subsequent catastrophic failure.
In a sense, the problem is caused by running the motor in its most efficient way: increasing motor speed boosts power and efficiency, without having to increase current or torque. However, increasing the speed also increases voltage frequency, which leads to electrical discharge.
The sensible answer is to use a ball bearing that is naturally insulating and will not conduct a current.
Ceramic balls
Switching conventional steel balls for their ceramic equivalent, to make a so-called hybrid bearing, is a recognised way of solving this problem, because the ceramic balls are naturally insulating. However, due mainly to their higher cost, only a small number of EV designers incorporate hybrid bearings in their designs.
At SKF, we estimate that only around 5% of bearings in these applications are hybrid ones. Typically, these hybrid bearings have only been specified because of the earlier failure of steel bearings in these applications. Very few EV designers specify hybrid bearings from the beginning, but we see that this is beginning to change.
The main reason that designers will not design in hybrid bearings from the start is that they cannot justify the extra cost. They are generally unable to predict the failure of the conventional bearings, so prefer to run them until they fail.
However, some of the larger EV manufacturers use sophisticated simulation software to model the exact conditions experienced by bearings in these applications. Using this software, they are able to see, and quantify, the amount of current leakage and its likely effect on the bearings. If it makes financial sense, they will replace conventional steel bearings with hybrid ones. Around five years ago, hybrid bearings were rarely designed in from the start. Now, it has become more common, and is likely to increase further.
Replacing conventional bearings with hybrids is generally painless, as the hybrid bearings have identical dimensions to conventional steel bearings. At the same time, the necessary design amendments, to the cage and grease, will already have been made.
In addition to their insulative properties, ceramic balls have other advantages: they are 40% less dense than their steel equivalents, which means they can run at cooler temperatures; they can have up to 10 times the life expectancy; and they require less lubrication. These advantages go some way to explaining their higher cost.
One premium user of SKF’s hybrid bearings is an automotive customer, who first specified SKF’s hybrid bearings back in 2014.
As well as resisting the effects of arcing, the hybrid bearings ensured higher efficiency, due to their lighter weight and greater hardness. Overall, the higher efficiency helps EVs travel further on a single charge, a key criterion of success as EVs compete with conventional cars.
Into the future
There is no escaping the fact that hybrid bearings are expensive. At SKF, we are looking into alternative solutions, and developing a way of solving the problem of electrical damage to bearing, but without using ceramic balls.
The answer is to create another path for the current, so that it does not pass through the bearing itself and damage it. At the moment, this technology is still under development, so we do not yet have any specific details to share.
There is another reason for developing this new technology: despite their huge advantage, ceramic balls do not completely solve the problem of current leakage. While they resist the effects of surface damage, the current can still work its way to the gearbox and cause damage there, such as by destroying the spline connection. We expect our new development, which is due to be launched by the end of this year, to solve this problem while also being cheaper than using a hybrid bearing.
SKF is not married to any particular technology but provides specific solutions to design problems. Right now, our hybrid bearings can help overcome problems of current leakage in EVs; soon, we will have a new technology that promises to do the same, but at a lower price.
We supply products such as bearings to most EV manufacturers in the market. So already have a deep insight into these applications and know how to solve their associated problems.
Looking further forward, some EV manufacturers may be able to overcome the problem of current leakage completely. If they are responsible for designing the full system, which is the case with some of the larger manufacturers, they will be able to ‘design out’ the problem at the source.
For other manufacturers, who may design the motor, but source other components such as the control unit and gearbox externally, this will be impossible, and they will need to continue using solutions such as hybrid bearings.
Electric vehicles are the way ahead for transport. Though they still account for a relatively small part of the market, making them as efficient and reliable as possible. Through the design of components such as bearings, will help to take a larger share of the market.