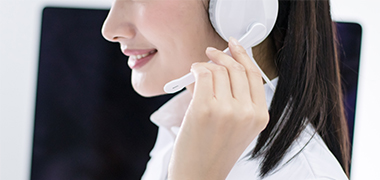
- Contact:Minister Xu
- Mobile:13841408476
- Tel:024-44837288
- Fax:024-44837004
- E-mail:xuming58@126.com
- Web:natashaterry.com
- Address:No.110 XiangHuai Road
Benxi Economic Development Zone
Liaoning Province
Finding fault: determining the true cause of premature bearing failure from SKF
03 Jul,2019
Premature bearing failure is often blamed on ‘white etching cracks’ – but looking deeper for the true underlying cause will lead to a more effective solution, says Erik Vegter, Senior Scientist for Fatigue Modelling and Testing at SKF.
Modern manufacturing practices, and techniques such as predictive maintenance, have helped to make premature bearing failure a rare occurrence. However, it can still happen and, when it does, can have a catastrophic effect. The most worrying thing is that some failed bearings are nowhere near the end of their calculated lifespans and may only have operated for 5-10% of their rated life. This is a source of great expense and annoyance to customers, who expect their bearings to last for their calculated lifetimes and beyond.
Some applications, such as wind turbine gearboxes have shown to be more prone to early bearing failure than others. The important thing for customers is to diagnose the failure and correct it. However, there has been plenty of debate over the exact causes of early bearing failure.
One common feature of premature failures is a network of small, white decorated cracks below the surface of the bearing, so-called ‘white etching cracks’ (WECs) or small axial cracks visible at the raceway surface (fig. 1). At first sight, it makes sense to assume that these are the cause of the problem, as they are seen in most cases of premature bearing failure.
However, an extensive, four-year research project carried out by SKF has shown that in reality these cracks occur at the end of the failure chain and are a natural consequence of crack networks in prematurely failed bearings. The company’s specialists concluded that WECs are only a visible symptom of the failure, and not part of the underlying cause.
SKF has so far identified seven mechanisms that cause premature bearing failure, leading to one common result: shorter bearing life as well as the appearance of WECs. As a consequence, SKF has developed a scheme to classify premature bearing failures (fig. 2), to help application engineers work together with customers to find the true root cause of the failures and, consequently, the most appropriate solution.
Despite this new insight, some premature failures are still being assigned to WECs and resolved on that basis (usually by replacing the failed bearing with an identical one). However, rather than needlessly repeating this approach, it is vital to drill down into the problem and pinpoint the underlying reason for failure. The SKF research has identified a series of underlying causes, allowing more accurate solutions to be found in each case.
Project details
The project involved replicating the exact conditions seen in bearings that failed in the field and subjecting them to extensive laboratory tests (including optical and scanning electron microscopy, and ultrasonics). Making the bearing fail under controlled conditions, helped SKF to pinpoint exact failure mechanisms, allowing a more accurate and targeted solution to be found to each problem.
For each root cause, SKF systematically reproduced the critical operating conditions on a test rig. This allowed them to know for sure which particular conditions caused WECs and allowed a link between the cracks and, for instance, structural stresses to be proven. The project has allowed SKF to clarify the role of WECs in relation to both classical bearing rolling contact fatigue and accelerated fatigue (accelerated spalling of bearings).
In bearing rolling contact fatigue (where there is no premature failure), WECs are generally caused by cyclic stresses and loading. However, the more extensive appearance of WECs is seen in accelerated fatigue, which can variously be assigned to higher stresses, lower material strength and/or a mixture of friction and lubrication effects (Fig. 3).
WECs are cracks within the microstructure of bearing steel. They are so named because of the white appearance of the altered microstructure of a polished and etched steel sample. The affected areas incorporate ultra-fine, nano-crystalline, carbide-free ferrite, or ferrite with a very fine distribution of carbide particles. White etching areas (WEAs) are formed by amorphization due to friction at the crack faces during over-rolling. These areas appear white under an optical microscope, due to their low-etching response to the etchant. White etching areas around cracks are 10-50% harder than the surrounding (and unaffected) microstructure.
Classification scheme
SKF has developed a scheme to classify bearings failures using its new approach (Fig. 2). This helps to suggest a particular solution, based on the more accurate diagnosis. For instance, if the failure was caused by lubrication problems or tribochemical effects, SKF may recommend moving to a black oxide coated bearing. Other failure modes, when identified, may lead to recommending solutions ranging from high strength stainless steel to hybrid bearings.
Overall, the research has been well received, with only minor disagreement on some of the details. There is certainly no debate on the main thrust of the argument, that white etching cracks come about through different failure modes. However, there is still more work to do: SKF has not yet replicated the conditions under which bearings fail due to electrical currents, for example, and so these experiments are ongoing in the company’s laboratories.
Solutions
The focus on finding new failure modes has now shifted towards developing better solutions. Through increased research and development, SKF is looking for the best materials and heat treatment combinations that can better cope with each failure root cause.
As well as developing a list of underlying causes for failure, SKF has come up with a range of general recommendations, based on the categorisation of the weakening drivers into ‘higher stress’ and ‘lower material strength’. The recommendations distinguish between those for the application itself, such as the bearing system or the design process, and on the possibilities to further increase bearing robustness. The option that is most effective in preventing premature failure will depend on the specific circumstances of the application.
In wind turbine gearboxes, SKF black-oxide bearings (fig. 4) have meanwhile proven to be a robust solution in this challenging application. Black-oxided bearings are delivered in high volumes to the wind market for more than a decade, on the most critical bearing positions to all major gearbox manufacturers and a very low failure rate has been reported (< 50ppm, based on more than 260 000 bearings in the field).
The robustness increase of black-oxide can be explained by the unique combination of properties countering the most severe operating conditions in the gearbox. Lab tests have shown a better performance in poor lubrication situations and high slip conditions because the treatment delivers improved lubricant adhesion and enhanced smearing resistance. The risks of fretting, micropitting and cracks can be limited. Resistant to corrosion and chemicals, black oxide bearings reduce the effects of moisture and aggressive oil ingredients. They also help improve friction behavior and reduce wear, particularly under mixed friction conditions which are present in wind gearboxes.When running under proper lubrication conditions, field examples have shown that the black oxide layer looks nearly intact after several years of operation, even in the low speed section (fig. 5)
Each premature bearing failure is unique and there are many potential reasons for premature spalling. There is no single root cause, and each failure case must be reviewed according to the relevant operating conditions. Understanding this and moving away from a diagnosis of white etching crack failure will help to ensure more accurate diagnosis of the problem, and a speedier solution.