Company News Industry News
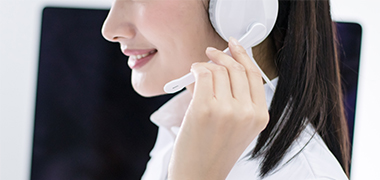
- Contact:Minister Xu
- Mobile:13841408476
- Tel:024-44837288
- Fax:024-44837004
- E-mail:xuming58@126.com
- Web:natashaterry.com
- Address:No.110 XiangHuai Road
Benxi Economic Development Zone
Liaoning Province
Taking a Bearing out at Sea
17 May,2019
Sulzer’s training for offshore projects ensures its engineers can deliver repairs quickly and efficiently
Bearing vibration in an offshore 4 MW thruster motor fixed through a joint effort. Large marine thrusters are vital for the safe maneuvering of vessels but their location on board can make maintenance a considerable challenge. So, repairing a failed bearing and housing on an offshore accommodation vessel would require technical expertise as well as innovative and flexible repair procedures.
Working in the North Sea oil fields, the conditions can be far from favorable, so a safe and pleasant living environment is essential to all offshore workers. Accommodation vessels are co-located with drilling rigs to provide living and recreation facilities for the crew.
The semi-submersible accommodation vessel is designed to house up to 450 personnel. It uses a dynamic positioning system, DP3 in this case, as well as a 12-point mooring arrangement to hold position at sea. The thrusters are a vital part of the positioning system and need to be maintained in perfect operational condition.
The primary maintenance contractor contacted Sulzer reporting high vibrations in one of the main thruster motors, which are located in the pontoons after the original equipment manufacturer (OEM) was unable to support the maintenance request at short notice. The project required the bearings to be inspected and replaced as necessary before recommissioning the thruster motor.
Since this type of repair had never been carried out on this vessel, it was essential that Sulzer carefully surveys the motor and its location before creating a risk assessment and method statement in line with the vessel’s operational guidelines. The site survey also identified all the tooling and access equipment that would be required to complete the repairs.
The highly-skilled site engineering team, based at Sulzer’s Aberdeen (Dyce) Service Center, put together a detailed plan for completing the project, before flying to Kirkwall in Orkney. From here, the engineers traveled by boat to the vessel and boarded by boat-to-boat transfer.
Once on board, it was apparent that access to the motor would be quite a challenge, with its location in a confined space and the close proximity of bulkheads. The project would require a well-planned procedure to achieve the bearing replacement.
The first task was to disconnect and remove the drive coupling, which was accomplished using the latest technology in induction heating. Jim McClean, Site Services Divisional Manager in Aberdeen, explains: “Heat is required to relieve the interference fit between the coupling and the motor drive shaft. In a workshop environment, this would be achieved using gas torches, but due to safety concerns this equipment was prohibited.
“With so much of our work being offshore, we needed a quick and safe method of heating components, and this led us to use specialist induction heating equipment. The system we use has been developed specifically for use in offshore applications and it saves a significant amount of time during repairs such as this one.”
Due to the vertical orientation of the motor, the Sulzer engineers could only repair one end at a time to ensure the rotor was supported during the work. The non-drive end (NDE) bearing was replaced and all the surfaces were inspected and found to be in good condition.
The drive end (DE) bearing was inspected and found to be pitted, and the outer race had been rotating in the housing causing it to also be damaged. As a result, the affected parts were removed for repair.
The damaged housing was immediately shipped to Sulzer’s Falkirk Service Center, where the machine shop applied metal spray to build up the damaged areas before machining it to the original OEM specifications – all within 24 hours. While the mechanical repairs were being completed, the site engineers on the vessel carried out the electrical tests that had been agreed with the vessel’s owners.
Once the repaired housing was back on board, the Sulzer engineers rebuilt the motor and reconnected the driveshaft before recommissioning the thruster and taking vibration measurements to confirm the effectiveness of the repair.
Jim McClean concludes: “Working in the offshore environment requires considerable expertise and qualifications as well as a liking of less conventional forms of transport. The customer was keen to repair the thruster motor as quickly as possible and that led to the conversation with Sulzer. With well-equipped facilities and the capacity to work around the clock, we have minimized any downtime and delivered a challenging project on time.”