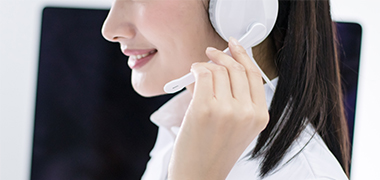
- Contact:Minister Xu
- Mobile:13841408476
- Tel:024-44837288
- Fax:024-44837004
- E-mail:xuming58@126.com
- Web:natashaterry.com
- Address:No.110 XiangHuai Road
Benxi Economic Development Zone
Liaoning Province
Bolt system resists effects of vibration for safer joint design
18 Feb,2019
It is vital that joints holding sub-assemblies together remain secure. Bolts need to be easily removable during maintenance, but resist loosening effects of vibrations and dynamic loads. Csaba Madru reports.
Ever since the bolt was invented it has been important to prevent self-loosening. Under static load the bolt is kept in place by frictional force under the head and in the thread. However, bolted joints exposed to dynamic loads or vibrations are likely to gradually loosen. This problem compels designers to use various kinds of bolt-securing methods.
Mentioning all known bolt-securing systems would result in a lengthy list. Even if some of the common bolt locking methods (such as serrated washers, adhesives or deformed nuts) work fairly well when the dynamic loads are lenient, only one method has proven fully reliable when conditions are extreme. If the cost of breakdown is high, maximum safety is crucial and quick and easy maintenance required, the Nord-Lock bolt securing system is superior. The technique utilises tension instead of friction to secure bolted joints. The wedge-locking method meeting DIN25201 outperforms any traditional method.
Make the bolt self-locking
For more than 20 years the specialist company Nord-Lock AB has produced a high-quality bolt securing system, consisting of a pair of pre-assembled washers (Fig.1). The washers have a cam angle 'a', which is greater than the thread pitch 'b'. In addition, there are radial teeth on the opposite sides of the washers.
The washers are always installed in pairs, cam face to cam face. When the bolt or nut is tightened the teeth grip and seat the mating surfaces. The Nord-Lock washers are locked in place, allowing movement only across the face of the cams. Any loosening attempt of the bolt/nut to rotate loose is blocked by the wedge effect of the cams (Fig.2).
Clamp load
When faced with a problem joint, it is not surprising that the design engineer will not have an answer when asked about the clamp load. Calculations must be based on the existing conditions and these are very vague. If all the parameters are not exact the torque calculation will be unreliable.
Examples of these parameters are: thread condition; hardness of the mating surfaces; extra friction from a 'locking' fastener; type of mating material (steel, aluminium, etc.); adhesive on the thread; oil or grease on the thread; moisture on the surfaces; type of bolt head (flanged, regular or serrated); surface coating of the bolt; new or used fastener; friction coefficient of thread, nut and bolt head.
Control over the clamp load in a bolted joint is vital. To achieve that the friction on the bolt should be low which in turn will result in a minimum of clamp load deviation.
In major automotive companies, incoming fastener batches are tested on the actual material of any specific joint to obtain the torque/clamp load ratio and its deviation. Their engineers know the clamp loads in the joints. Smaller- and medium-size companies are usually not in possession of sophisticated bolt testing laboratories.
Failure
Some of the many reasons for machine failure due to bolts coming loose or breaking are:
- In principle, the bolt is designed to hold due to its own friction in the thread and under the head. This works during static conditions but not when there are high dynamic forces. Especially transverse dynamic loads are dangerous.
- The thread pitch can be compared with a down hill slope where thread slip occurs.
- The clamping length could be too short so that any motion in the bolt will result in a severe loss of tension.
- When re-using bolts without lubrication, the friction can be very high, resulting in a very low clamp load.
- Re-using bolts initially locked with adhesives with higher friction and a very low clamp load as a result.
- Loss of clamp load due to bearing surface being too small leading to fatigue failures.
Various studies have been done in Nord-Lock's test laboratory on torque/load ratios and vibration tests on specific joints.
During regular testing of customer's applications, it has been noticed that illogical measures have been taken with the purpose of achieving higher bolt security. It often happens that an engineer chooses a high-grade bolt for a joint that has had bolt failures with a standard 8.8 bolt.
Unfortunately, the surface treatment on high-grade bolts compared with normal electro zinc-plated may change the friction conditions which should be taken into consideration when calculating the torque figures.
In addition there is a risk of over-loading the base material of the joint. Even with a higher torque value, the clamp load may be too small due to the higher friction. The joint becomes more expensive but not safer.
Other bolt securing systems
Locking nuts: A survey of bolt securing systems will show a large number of different locking nuts, which try to hold onto the thread through increased friction. During vibration tests with transverse motions according to the Junker Principle, meeting the German standard DIN65151, there is a loss in preload of 80 to 90 per cent at a given amplitude. That means, the securing nuts do not fall off the bolt, but they do not prevent the bolt from starting to rotate and from loosing most of its preload.
Any of these nuts show more or less the same result. The pitch of the thread always makes the nut turn at a certain amplitude of transverse motions. The greater the amplitude and the shorter the clamping length, the quicker they start turning.
Tab washers, safety wire and castellated nuts: Old-fashioned securing systems such as tab washers, safety wire and castellated nuts are still widespread. These methods are very expensive and labour-intensive, plus they will not provide a firm locking since the tab, wire, or pin is of soft steel. When using tab washers there is always a risk of moving the nut/bolt during assembly, resulting in a loss of preload.
Furthermore, if the tab is not exactly parallel with any of the sides of the bolt head, it may start rotating when exposed to vibrations or dynamic loads. Even insignificant rotation of the bolt/nut may cause a significant loss of preload.
Spring washers: It is a misunderstanding that spring washers have a locking effect. Most spring washers only add a minute amount of spring action (up to 10 per cent of the capacity of a grade 8.8 bolt). If serrated, there will be an increase in friction, which may result in a locking effect which normally does not last when exposed to vibration or dynamic load.
Customer support and safety tests
Nord-Lock AB has a well-equipped test laboratory located in Malmo in the south of Sweden. Here clients can put joints from their own applications to the test. In simulations of real-life conditions torque-load ratios are measured and Junker vibration tests are performed.
In a Junker vibration test (meeting DIN65151) bolted joints are subjected to transverse movements while a load cell continuously measures the bolt tension. The Junker test is used to compare different bolted joint configurations and is a first step in selecting the best technical solution to prevent bolt loosening. The Junker test is sometimes considered a worst-case scenario and bolted joints performing well in this test normally function flawlessly in real life conditions.
Fig.3. shows the bolt tension during vibration testing of some common fasteners. The entire bolt tension is lost in unsecured joints while most of the tension is lost in joints secured by thread friction nuts.
Vibration tests
All vibration tests with Nord-Lock show a positive result. Nord-Lock washers prevent any rotation of the fastener and only a limited part of the initial bolt tension is lost due to normal settlements between the contact surfaces. Nord-Lock's wedge-locking function is verified by increase in tension during untightening.
Nord-Lock washers can be used for slotted-hole applications. The use of special (sp) washers with enlarged outer diameter in combination with a flanged bolt/nut is recommended to increase the load area as much as possible.
Normally also standard Nord-Lock washers lock the joints but enlarged washers are more lenient to the contact surfaces (Fig.4).
The total stress in a bolt is called equivalent stress, which consists of tensile stress and torsion stress according to the formula.
Equivalent stress = 1 sx2 + 3 txy2
Any given bolt can only withstand its maximum yield stress. In order to maximise the tensile stress (sx) it is vital to minimise the torsion stress (txy). This will require a lubricant on the thread. The safest method is to apply thread paste or thread grease. Additional positive effects from this lubrication are that the deviation of clamp load will be reduced significantly and after a long period of time it will be a lot easier to dismantle since the lubricant will offer a corrosion resistance.
Clamp - load curves from tightening bolts during different thread friction conditions are shown in Fig.5.
Advantages
For machinery requiring regular service and maintenance, Nord-Lock is the optimum solution. Bolted joints secured with Nord-Lock are easily assembled and disassembled and no special tools or fasteners are needed. Since the Nord-Lock bolt securing system uses tension instead of friction to secure bolted joints the locking function is not affected by lubrication. The use of a good lubricant is recommended in order to reduce friction, minimise clamp load deviation and to protect against corrosion.
Stud bolt securing has been truly improved with Nord-Lock. Common practice when securing a stud bolt is to lock the stud in the tapped hole with an adhesive and use a jamming type nut.
This method is unnecessarily complicated and difficult repair work can be expected should the bolt break as a result of fatigue. Stud bolts with the same thread pitch in both ends will not turn or loosen even if lubricated and the nuts can be safely secured with Nord-Lock washers. The elimination of adhesives significantly facilitates repair jobs (Fig.6).
Range and applications
All Nord-Lock washers are produced in compliance with the RoHS and ELV directives. Washers are available in steel with zinc flake coating for bolts from M3 to M130 and in stainless steel from M3 up to M80.
Nord-Lock washers have successfully solved loosening problems for more than 25 years. The system makes assembly easy and provides maximum safety.