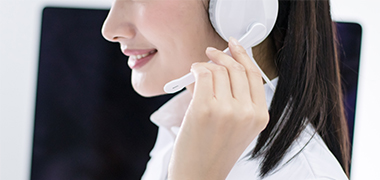
- Contact:Minister Xu
- Mobile:13841408476
- Tel:024-44837288
- Fax:024-44837004
- E-mail:xuming58@126.com
- Web:natashaterry.com
- Address:No.110 XiangHuai Road
Benxi Economic Development Zone
Liaoning Province
BUILD A STRONGER MODEL 20 AXLE
29 Jan,2019
The AMC Model 20 rear axle was at one time a common component in Jeeps, some American Motors cars, and as IFS/IRS differentials in the Hummer H1. Easily identified by a round cover with 12 bolts, inside is an 8 7/8-inch-diameter ring gear. Stock gear ratios ranged from 2.56:1 to 4.10:1, and aftermarket cogs are available up to a 4.88:1 ratio. Spline count on the shafts was 29 splines. There was also a narrow-track AMC 20 used in Jeeps from 1976 to 1981; it measured 50.5 inches from flange face to flange face. A wide-track version of the axle was used from 1982 to 1986; the axle width was increased to 54.4 inches.

The AMC 20 axle was delivered from the factory with a two-piece shaft design. While some of these axleshaft assemblies have survived fine for decades, some others have failed when the splines between the axleshaft and the mating wheel flange shear, causing the hub to spin on the shaft. Long-term wheeling or larger tires can bring on this failure, resulting in the loss of drive to the tire connected to that axle.
The relatively weak welds where the pressed-in axletubes mate with the centersection of the housing are another vulnerability of Model 20 axles. These welds can break and cause the axletube to rotate in the centersection. Also, the axletubes are considered by many to be relatively weak, and some owners have retubed these housings with thicker-walled tubing.
Our 1976 CJ-5 had the stock narrow-track AMC 20 axle and was still running the original two-piece axleshafts. We didn’t feel we needed to move up to a larger axle, but we did want to address several weaknesses in the current one. We aimed at running 32- to 33-inch tires and installed a one-piece rear axleshaft conversion kit (including high-tensile strength 4340 chromoly shafts) from Alloy USA. The shafts also use cold-rolled splines that are stronger than typical cut splines. Our stock differential cover was still straight, but we opted for a Rugged Ridge armored cover. This axle was already populated with an air locker and 4.11 gears, so we left the differential internals alone.
Removing and taking the stock axle apart was the first step. We needed to reuse the drum brake backing plates that were captive on the stock axles between the wheel hub and the pressed-on wheel bearing. A large jaw puller wouldn’t pull our two-piece axle assemblies apart, and we were unsuccessful pressing them apart on a shop press without doing damage to the backing plates. We finally cut apart the wheel bearing cages and dissected the taper bearings until the bearing assembly came apart. Then, the backing plate could be slipped over the remaining inner race of the pressed bearing.