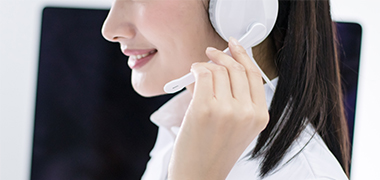
- Contact:Minister Xu
- Mobile:13841408476
- Tel:024-44837288
- Fax:024-44837004
- E-mail:xuming58@126.com
- Web:natashaterry.com
- Address:No.110 XiangHuai Road
Benxi Economic Development Zone
Liaoning Province
Thordon to provide bearings for LNG-fuelled cutterhead suction dredger
23 Nov,2018
Thordon Bearings Inc. has announced that it will provide the water-lubricated composite cutterhead shaft and intermediate ladder bearings for the LNG-fuelled cutterhead suction dredger (CSD), Spartacus.
The vessel is scheduled for delivery next summer to DEME Group – a Belgian dredging and reclamation specialist – from Royal IHC’s shipyard in Kinderdijk, the Netherlands. It will be able to cut harder soils and at faster speeds that it could previously manage. In addition to this, it will be the world’s first dredger able to operate in water depths of up to 45 m (147.6 ft). Currently, 35 m (115 ft) is the maximum water depth in which dredgers are capable of operating in.
Bart Bakker, Managing Director of Sandfirden, Thordon’s Netherlands-based distributor and engineering partner, said: “It is without doubt DEME’s experience of Thordon’s self-lubricating Composite bearing on the 123.8 m (406 ft) cutter suction dredger, D’Artagnan, that resulted in us securing this milestone order. When the D’Artagnan’s intermediate ladder bearings were removed for inspection in 2014 after nine years of operation, they showed practically no wear and were not replaced.”
For the CSD, Thordon provided Royal IHC with four composite intermediate ladder bearings for shaft diameters of 1400 mm (55 in.) – the largest diameter composite bearings ever produced by the Canadian company – and a single composite cutterhead bearing for a 1050 mm (41.3 in.) shaft diameter.
George Morrison, Thordon Bearings’ Regional Manager, Western Europe, Africa and Aus/NZ, said: “We are delighted that DEME Group has returned to Thordon with an order to equip this innovative and important vessel. The through-life performance of our composite cutterhead shaft and intermediate ladder bearings not only deliver longevity but compared to traditional arrangements, operational costs are much lower due to the longer periods between replacement, less downtime and the elimination of grease.”