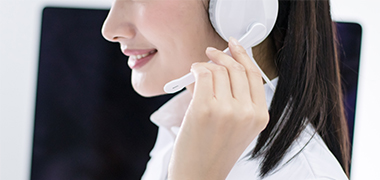
- Contact:Minister Xu
- Mobile:13841408476
- Tel:024-44837288
- Fax:024-44837004
- E-mail:xuming58@126.com
- Web:www.natashaterry.com
- Address:No.110 XiangHuai Road
Benxi Economic Development Zone
Liaoning Province
SKF and NREL work to improve wind turbine drive train reliability
02 Jul,2018
A joint investigation by SKF and NREL will establish a new benchmark for drive train validation with a view to reducing the cost of ownership of wind turbines.
SKF has entered a three-year collaboration with the U.S. Department of Energy’s National Renewable Energy Laboratory (NREL) to study the performance of wind turbine drive trains under a variety of conditions, and to gain insights into the possible causes of wind turbine bearing failures. The main purpose of this partnership is to investigate the failure modes of both gearbox and main shaft bearings, with the aim of developing new, improved designs for greater reliability.
The investigation work is being carried out on an existing GE 1.5MW turbine installed at NREL's National Wind Technology Center (NWTC) facility in Colorado, USA. SKF will contribute a variety of components and systems to the project, including the new optimised spherical roller bearing (SRB) 240/600 BC, bearing housing, seals, condition monitoring hardware and software (IMx-8 and @ptitude Observer 10.2), and an automated lubrication system.
Various sensors are installed for the measurement of atmospheric, static and dynamic conditions within the gearbox and main shaft bearing, while bearing stray currents will be monitored using a Rogowski coil based tool. The sensor measurements are expected to provide deeper insights into the causes of gearbox bearing failures, such as humidity, mechanical overload, stray-currents and roller slip. The SKF patented roller speed measurements, in particular, will provide a fuller understanding of the actual kinematic behaviour of the bearings in the turbine, without having to make significant bearing modifications.
The NWTC provides real world atmospheric and load conditions for the turbine, enabling the impact of high winds and variable grid loadings and faults on the turbine's mechanical systems to be studied. The long term data acquired from SKF's installed systems will be used to analyse the causes of bearing axial cracking on the high speed shaft and conditions that compromise main bearing reliability, both of which frequently incur excessive operations and maintenance costs for the wind industry.
The project gives SKF an ideal opportunity to get another validation for the performance of its new optimised SRB for applications within the wind energy industry. This work is supported by SKF’s Design Verification Support Tool, which helps to prove the capabilities of the main shaft bearing under actual running conditions.
An optimised version of SKF's standard SRB, the new main shaft bearing, features a modified internal geometry that delivers extended calculated life, lower contact pressures, a higher contact angle, improved osculation and minimised sliding contact for reduced wear. The cage is manganese phosphate coated for superior corrosion protection and the bearing internal lubrication performance has been enhanced.
Insights gained during this study period have the potential to improve both gearbox and main shaft bearing components, and provide a better understanding of how a turbine reacts to the most severe atmospheric and grid conditions. The shared vision and goals of SKF and NREL to address these drive train reliability issues will ultimately make a significant contribution towards the wind energy industry's efforts to reduce its costs while maximising its output and efficiency.